

In today’s highly connected world, corporations are taking full advantage of modern technologies to build more efficient workflows. German automaker Mercedes-Benz took things one step further when planning its newest production facility dubbed “Factory 56,” which is now showing off via a virtual tour.
The new facility will be located in Sindelfingen, Germany, and it’s slated to be home for a plethora of electric and gasoline-powered vehicles. Mercedes says that it will build its next-generation S-Class in that plant right alongside its upcoming EQ electric models, meaning that the facility is equipped to be completely modular in its production line flow.

Similar to Porsche, Mercedes will make use of up to 300 Automated Guided Vehicles (AGV) to transport cars and part bins, meaning that a traditional production line consisting of rails and pre-set paths are a thing of the past.
The 220,000 square meter facility will connect all aspects of the plant; from part picking to tools, the workflow and productivity are constantly tweaked, unbeknownst to the workers in order to make things run smoothly. Even torque wrenches can be adjusted on-the-fly to apply the correct amount of force based on part currently being assembled. If an employee makes an error in assembly, the automated systems will alert the worker and provide instructions on how to fix the problem.
Though this may seem like robots are taking over the entire production process, the automaker stresses that it will use automation only where appropriate, a lesson learned earlier this year when it changed the production flow of the high-end S-Class.

Digital tracking of all parts helps Mercedes to establish what it calls a “Smart Supply Chain”, meaning that the automaker can track parts from their source factory of origin to the vehicle which they are placed in. This connected feature will carry the added benefit of enabling customers to make last-minute changes to their order, prior to the part being placed on the vehicle. We imagine that it will also help to cut down substantially on recall efforts, should it be required, by tracking which cars certain affected parts end up in.
Mercedes is also committing to making the plant run as green as possible, touting that its goal is to make a facility that operates completely carbon-neutral. It plans on achieving this by utilizing a roof-mounted solar farm, similar to Tesla, which will power everything from day-to-day operations as well as on-site chargers for its electric cars. The facility will also be primarily lit using skylights to reduce electricity consumption. Mercedes insists that its facility will be completely paperless, making use of digital displays to help reduce waste and present data.
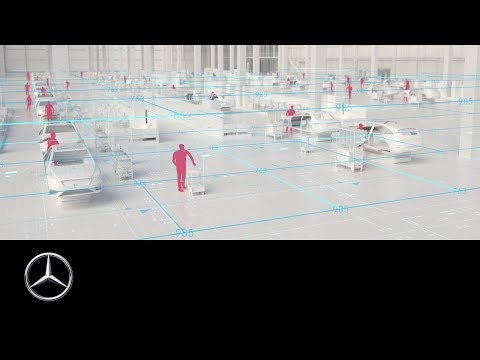
Sindelfingen, Germany has been home to a Daimler Motors Corporation plant since 1915 (Daimler and Benz merged in 1926). Right now, it only exists as a digital model, however, Mercedes has made use of virtual reality to give its facility a test run and is pleased enough with the results to greenlight the project. The automaker says that its new plant will be up and running in 2020.