

HRE announced Tuesday that it has built the world’s first set of 3-D printed titanium wheels, showcasing the futuristic manufacturing method’s capabilities and potential.
Called the HRE3D+, the wheels are the result of a partnership between HRE and General Electric’s additive manufacturing subsidiary Arcam, who supplied the machines and technology with which the rollers were made. Arcam brought additive manufacturing expertise to HRE, which contributed knowledge of proper wheel design.

HRE took its CAD design for the HRE3D+ and split it into a series of two-dimensional layers. A machine replicated each layer, one at a time, with a small amount of titanium dust, a metal chosen for its strength and inherent resistance to corrosion, making it ideal for wheels. Arcam’s electron beam melted then fused the layer of dust together, and gradually, these layers built up, forming the spokes of the wheel.

After some minor machining to guarantee the spokes’ fitment to the central hub and carbon fiber rim, each spoke got a smooth decorative finish. HRE and GE detailed the entire manufacturing process in a video, which they released as part of the announcement.
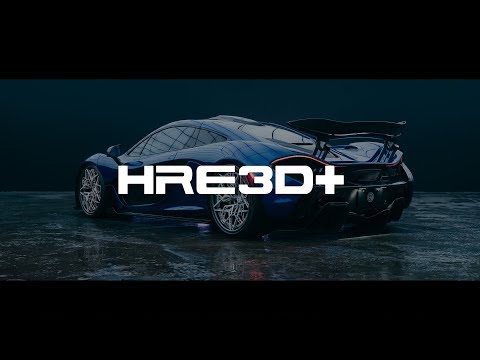
HRE built two pairs of wheels in slightly different sizes of 20×9 inches and 21×12.5 inches, front and rear, respectively. The resulting quartet of wheels was then shod in Michelin tires and bolted to a McLaren P1, where they somehow made the exotic hypercar look conservative by comparison.
HRE considers the wheel more a proof of concept and a technological showcase than something it can manufacture in large quantities, despite this process making more efficient use of material than subtractive manufacturing methods such as machining. A company spokesperson tells The Drive that less than five percent of material is wasted with this manufacturing process, as opposed to around 80 percent with forged and machined wheels.
In time, HRE hopes that additive manufacturing can become a commercially-viable manufacturing technique, one that can allow it to offer wheels manufactured in this fashion as part of its product lineup. Larger EBM machines will enable HRE to manufacture the wheel’s spokes together, as opposed to the HRE3D+’s individual spokes, which will allow construction of a three-piece, 3-D printed wheel.
HRE makes no mention of what these wheels actually weigh, or how much they cost to produce—the latter could at present be the biggest hurdle between this style of wheel and the mass market.
It’s not just the aftermarket that’s exploring the possibilities of additive manufacturing, though. Both General Motors and Volkswagen tout the virtues of 3-D printed parts, which allow radical improvements to their design, or even low-cost personalization. Even BMW is in on the 3-D printing fun, but for a radically different purpose: Inflatable 3-D printed interiors.