An 11,230-RPM LS7 V8 Is Pure Madness You Need to Hear to Believe
It’s called “Project Spinal Tap” because this one goes to 11…thousand.
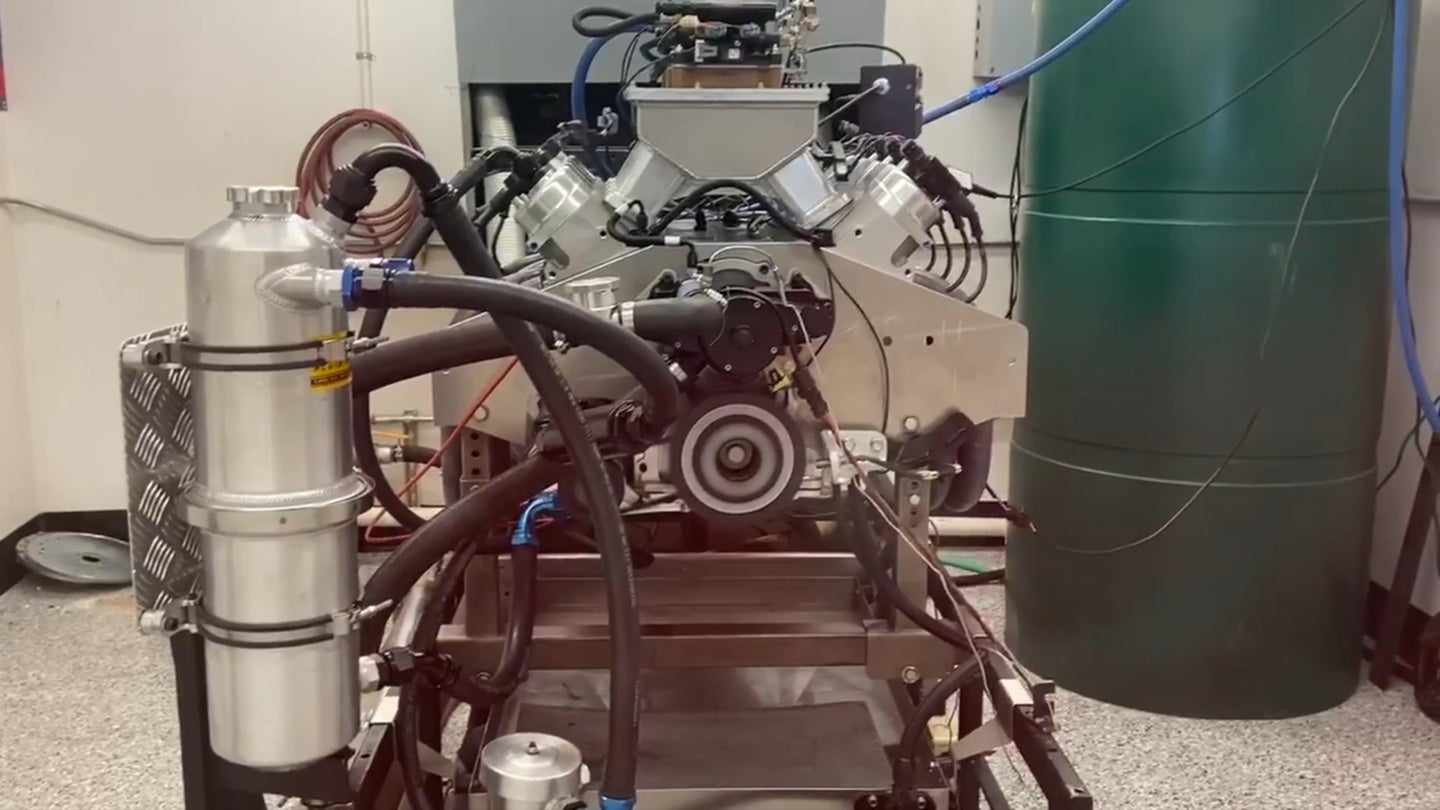
EFI University's Benjamin Strader had just one goal: to get a GM LS V8 engine to hit 11,000 RPM reliably. The stock redline on an LS7 crate engine is 7,000 RPM, but clearly that's not enough. "Project Spinal Tap" wanted more. And Project Spinal Tap's only reason for existing is to go to 11 thousand RPM, of course.
"It was kind of a 'hold my beer' moment where we got talking about, could we take an inline wedge-headed LS7-based engine and make it go to 11,000 RPM," Strader explains.
Strader admits in this video that the engine was birthed as just an experiment to see whether a modified LS7 can exceed 11,000 RPM reliably on a dyno. Its peak power is still probably around the 9,200-9,400 RPM range with a drop-off as the engine spins faster, so tuning those higher revs for power will have to come later. We've seen other high-revving LS builds with redlines in the 9,200 RPM range, so this makes sense.
The engine Strader and his collaborator Billy Godbold ultimately built is a 5.8-liter beast that cranks out 921 horsepower at 9,300 RPM and 545 lb-ft of torque at 8,000-8,200 RPM, notes EngineLabs. Godbold is also no stranger to high-horsepower LS builds, as he is Comp Cams' chief cam designer.
LSX Magazine has a fascinating deep-dive into what allows Project Spinal Tap to move so fast. The meaty, 114-pound Dart LS Next iron block used as the basis for Project Spinal Tap has a Brinnell hardness rating of 220 BHN, compared to the 180-200 BHN found in regular cast iron blocks. The 16 Manton pushrods are also massive to handle the extra torque, weighing 6.2 pounds in total. The crankshaft itself was made by Winberg out of billet 4330V-steel, which included a bit of vanadium in the alloy for extra strength. The highest-stressed parts of this build were the M10 CARR rod bolts, which are rated for up to 285,000 psi.
Lubrication is key to something like this not melting itself apart. As LSX Magazine notes, Project Spinal Tap features a dry-sump to keep everything well lubricated throughout the massive rev range, and the six-stage pump for the system is integrated into the billet pan. Rods were piston-centered to leave extra room for better oil flow. Piston rings were extra thin and coated in titanium to reduce friction. Extra spray bars built into the billet valve cover also help lubricate and cool the valve springs. Nearly every component of this engine was tweaked to achieve this 11,000 RPM goal, and LSX Magazine's full how-to breakdown is really worth the read.
Firing it up after three years' worth of work was certainly a terrifying moment. There's just a window between Strader and his dyno room, and an engine spinning at 11,000 RPM could very well launch chunks into low Earth orbit if it breaks.
Strader says it took about a year and a half to two years just to get the valvetrain stable for this project. You can see one of the Spintron runs of that valvetrain above. Project Spinal Tap only continued after they were able to repeatedly test the valvetrain at over 11,000 RPM with no issues.
"I don't know if you can tell on the video whether or not I'm nervous, but I for sure am," Strader says before running his completed engine.
Fortunately, we got to experience the incredible noise an LS7 makes at even higher revs than ever before. The LS7 was revered at its launch for having the highest redline ever in a production pushrod V8—7,000 RPM—as Hot Rod noted at the time. So, it's about time to make those Spinal Tap-fueled RPM dreams happen.
[H/T Engine Swap Depot!]
Got a tip? Send us a note: tips@thedrive.com
