How Brembo Makes Brakes for Le Mans, F1, and Your Project Car
We visit the factory where all racing brakes from F1 to Le Mans and even aftermarket kits are manufactured.
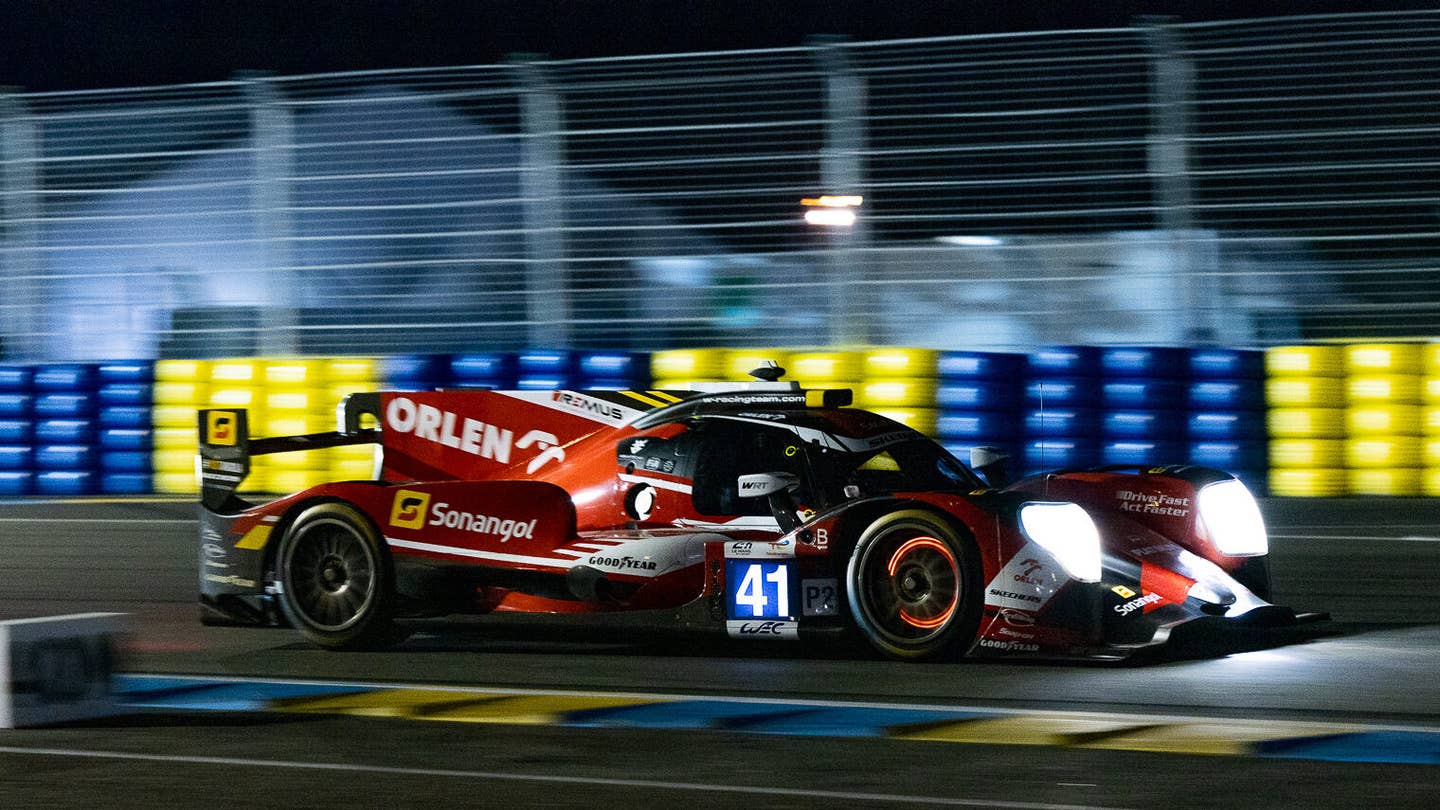
Brakes, much like tires, are largely considered an unsexy part of a car. They perform the task of ending the fun; they're the opposite of the thrill of acceleration and cornering. Any time someone goes to modify a car they always focus on going faster, but rarely on stopping sooner. In the toolbox of a racing driver, however, brakes play the most important role in nailing the perfect lap. Optimizing brakes to provide instant, modulable stopping power is one of the challenges brake manufacturers face. The other? Making them last. That one is the real challenge—and one that Brembo tackles with enthusiasm.
“We supply just around 90% of the Le Mans grid,” said Brembo racing engineer Mauro Piccoli while showing me around a bustling paddock at the Circuit de la Sarthe during the 2023 24 Hours of Le Mans. “We do everything. From the master cylinder and pedals to the caliper, discs, and pads.”
Brembo supplies its clients with two different kinds of braking systems for endurance racing: Carbon-carbon and iron. Regardless of the kind, they all come from the same shop located just outside of Milan.
24 Hours of Punishment
“Here, carbon brakes are not allowed,” said Piccoli gesturing towards the No. 54 AF Corse Ferrari 488 GTE in the garages. He began his next sentence when a group of GTE cars thundering down the front straight interrupted him. “Here we have to use iron-based discs, not carbon.”
There's a very important reason for this: costs. Using more basic technology keeps the cost down massively compared to high-tech, high-dollar carbon brakes. But according to Piccoli, the iron brakes can last 24 hours just as well as the carbon brakes thanks to the maturity of Brembo's technology, and the understanding of the materials involved in the components.
For example, you cannot over-cool a cast iron disc because it will crack. On the other hand, if you under-cool cast iron it will reach a critical point of heat rejection and won't absorb any more heat. This means the kinetic energy of the car has nowhere to go and that's a big problem when you expect your brakes to work lap after lap for 24 hours. This is the primary disadvantage of iron and steel brakes, where rotor weight dictates how much kinetic energy it can absorb. Carbon brakes have the advantage here and can work in a much wider window.
Racing carbon brakes are made completely from carbon, with no ceramic or silicon carbide to augment the material. Even the brake pads are made up of carbon fiber. Both iron and carbon brake systems use effectively the same style of caliper—which the FIA restricts to only six pistons for LMP2 and Hypercar. However, because races are won in the gray areas of the rulebook, Brembo’s more aggressive pocketing and milling work on the calipers represent additional weight savings while still meeting regulations. Carbon brakes are even lighter than carbon ceramics, which is what you'd find on most high-end street cars and even most track-specific sports cars. Lastly, carbon brakes represent close to 75% weight savings over iron brakes.
Unsurprisingly, the technology to produce them is highly proprietary. After Le Mans, I visited Brembo's shop in Bergamo, Italy where it produces its carbon-based brakes, and all of its racing brakes in general. Sadly, and as you can imagine, this place holds lots of trade secrets and I was not allowed to take photos of the manufacturing or assembly process.
How the Carbon Sausage Is Made
The immediate impression was of overwhelming manufacturing power, one that most other competitors do have, but isn't so singularly focused on brakes. Brembo does nothing else, whereas someone like ATE or Nissin makes several other parts for automakers. Most importantly, Brembo only does fixed calipers and doesn't touch anything else, such as the sliding calipers that you would see on a normal economy car.
Brembo doesn’t build factory road car parts in Bergamo. Instead, they do the research and development for those calipers and they're produced at a different facility. In the showroom, huge fixed calipers from nearly every automaker are featured, from Rolls-Royce to Honda, they're all proudly on display. Go through a few doors and a dark hallway, however, and a sprawling factory lays just beyond. This is where all of the world’s Brembo brakes destined for racing are made.
While the process of making iron and steel brakes is fairly straightforward, making carbon-carbon brakes takes a highly specialized facility and anywhere from six to nine months of work to make a complete batch of brake discs. It starts with cuts of carbon fiber weave that effectively feels like charcoal fabric in your hands. The pieces are cut into pizza-like slices, then layered over one another in a specific way until the required amount of thickness and density is achieved.
Those carbon fabric layers are placed in an extraordinarily powerful press to fuse them together, then carbonized off-site to turn them into a raw carbon brake rotor. The raw carbon discs return to the shop for a final quality check. If they pass, then they're turned into fully dressed carbon rotors ready for racing duty.
I was struck by how surprisingly quiet the factory was despite running at full steam. And also how the pace felt much calmer than the normal frantic sprint that defines most production facilities. Precision and patience are what's needed to make carbon brakes. Brembo is one of the few companies in the world with the knowledge of how to make brakes of this caliber, let alone innovate systems around the production process. This vertical integration of making everything from start to finish is rare in the auto manufacturing business.
The completed rotors get carted off to a small team of about 40 people in a climate-controlled room. They assemble everything from F1 brakes to off-the-shelf big brake kits you can buy for your car. Included in that domain are the iron and carbon brakes used at Le Mans. The brake systems get hand-assembled from the caliper, rotor, pedals, and master cylinder into a complete system. They’re then bench-tested, relentlessly checked, and then go through another round of quality control. From there, they’re packed away and sent across the world.
Testing and Validation
Developing everything from scratch takes a huge apparatus of people, facilities, and institutional knowledge. Not far from the manufacturing facility in Bergamo is the “Kilometro Rosso.” Named for being a red building that is a kilometer long, it is most notable for being Brembo’s research and development hub for racing and road car systems. Parts are tested on full-suspension rigs that simulate being mounted to a car, then finally tested on the road via a secret workshop out back that is Brembo's equivalent of Area 51. Automakers send small teams of engineers and prototype cars there to get hands-on testing with Brembo on-site.
The might of Brembo is hidden in the sprawling buildings, which somehow felt bigger than the facilities that produce the parts. There were dozens of engineers drafting away on brake systems in one huge office, and right next door there was a row of a dozen brake calipers on benches running for weeks at a time for durability testing. Unfortunately, I was not allowed to take photos of the top-secret operations within the facility.
Right next to that was a room full of temperature- and humidity-controlled ovens that ran calipers to their limits to verify function under all weather conditions. In another room deep within the fortress, there’s a fully equipped laboratory with a small team of people in white coats figuring out ways to optimize metallurgy, brake pad compounds, and brake fluid. That place is also home to a $2-million electron microscope used to examine failures and material structures at a molecular level.
Then there's dynamic testing. Brembo uses both bench and full-suspension rigs to test brakes. While performance and durability testing is done on the bench rigs, automakers ship Brembo full suspension assemblies from the innermost control arm mount outward to test on modified rolling roads. This is to make sure that no braking components cause an unexpected harmonic response and to verify vibration on the real assembly.
Finally, those parts get put onto prototype cars and driven to the nearby Autodromo Internazionale di Monza for track testing. From there, final signoff, then off to production on almost any number of cars and SUVs you see with a fixed brake caliper.
This Is What It Takes
From master cylinders to rotors, calipers, and brake fluid, Brembo doesn't manufacture anything else. Normally, this would confine a supplier into a fairly small operation, but Brembo has the market share to rival the biggest suppliers in the business. Think about it, seeing "Brembo" on a caliper is a bit of a status symbol, and certainly a huge cool factor for enthusiasts.
What was absurd about visiting their home base was the sheer size of the operation and the fact that it genuinely makes just about everything in-house. Typically, if Brembo isn’t written on the brakes it’s often cast into the caliper out of sight.
This is what it takes to make a crucial component for the vast majority of the Le Mans grid and the high-performance sports car segment. It’s top-to-bottom control over engineering, manufacturing, and design. Even more special is that this knowledge genuinely translates into brakes you can buy for any road car as an aftermarket option. Should you buy a Brembo Big Brake kit, there’s a chance the same person who put together Charles Leclerc’s brakes for his F1 car also worked on the shiny new brakes for your project car.
The automotive scene is changing, however, and Brembo is looking to the future with new solutions in brake pads, rotors, and fluid offerings, as well as development on "Sensify," its fully brake-by-wire system that gets rid of most or all brake fluid lines.
So while you can’t quite get Le Mans-winning brakes on your road car, you can have a slice of that technology from the same people. Brakes can be unsexy, but for the discerning enthusiast, there really is nothing better than seeing a set of brakes filling out the wheels of their performance car.
Email the author at chris.rosales@thedrive.com
