How To Build A 1930 Ford From Swap Meet Parts, Part II
Ben Preston joins a crew at the Hershey swap meet assembling a Ford Model A from parts scored there.
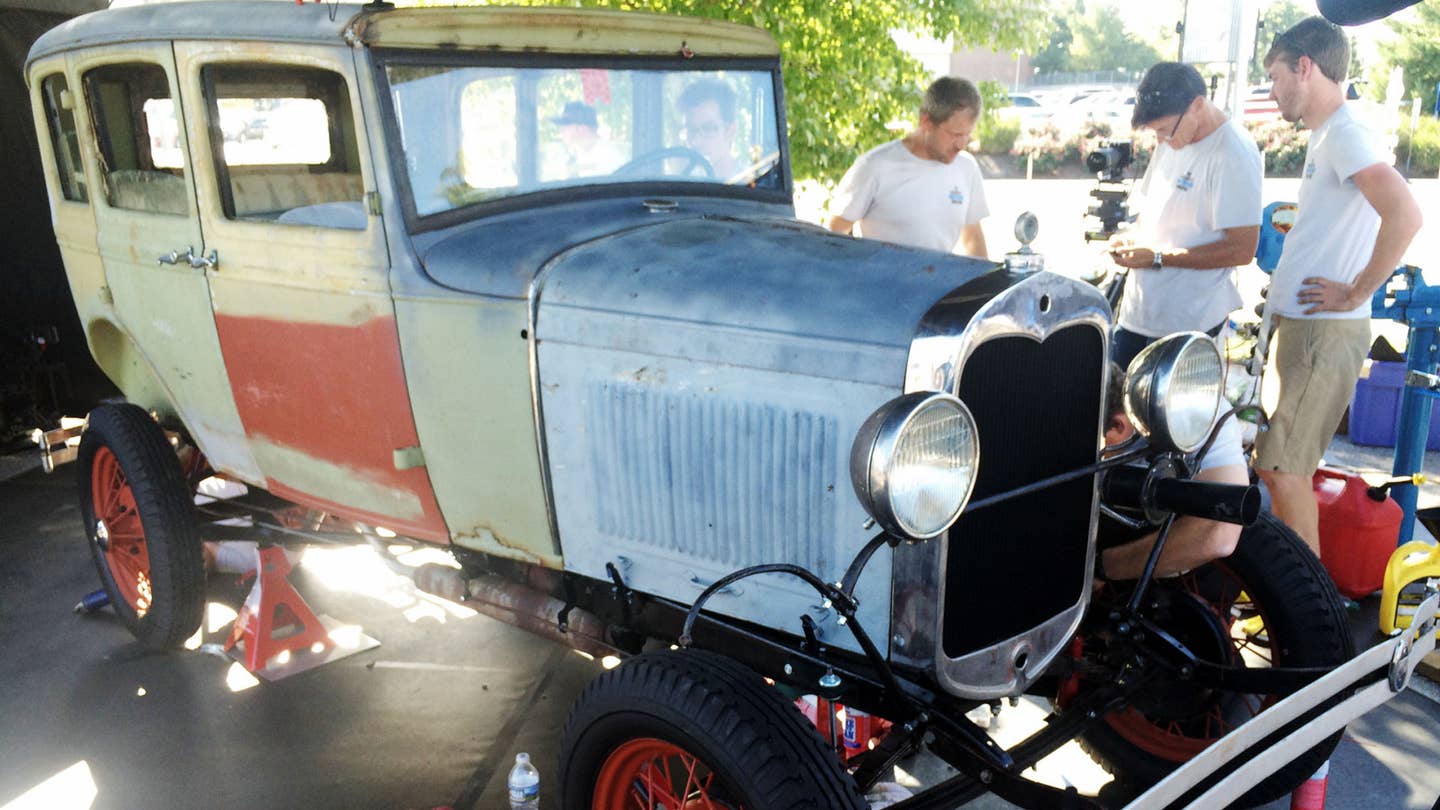
By the dawn of their second day of actual wrenching, the Hagerty crew had turned a pile of parts into something that looked like a car. At the end of day three, they were able to move that car, a 1930 Model A Ford they were building for this year's Swap to Street Challenge, under its own power from the beneath tent where it had come together.
The team had arrived in Hershey, Pa. for the annual car show and swap meet on a Tuesday. By Friday, they were driving it around the parking lot to the whoops of a crowd of supporters that had gathered to watch the action. Of course, they still had a long way to go. As anyone who's ever built a car from parts knows, getting it running is only the beginning, really. With the car sputtering along, they still had to drive it more than 700 miles, on local roads, back to their headquarters in Traverse City, Mich.
Getting the car from parts pile to purring was labor intensive, but it was also pretty straightforward. Davin Reckow, who serves as Hagerty's parts supply specialist most days, was in charge of directing the build team. He was joined by Brad Phillips, the company's client relations manager; Randy Clouse, who teaches automotive knowledge to company employees; and Brett Lirones, the company's boat-policy specialist.
Reckow said that, to start, he looked for team members that would complement one another—skilled people who weren't afraid to speak up and say, "Hey, what's next?!"
"If you have somebody who's gonna stand back and wait to be told what to do, that's tough to work with, especially when you're in a big crunch," he explained. "Everybody's gotta understand the crunch and that push toward getting the project done."
In fact, they were all so wrapped up in their individual tasks, they stayed focused until the engine fired for the first time. As soon as that brief excitement was over, they all had their noses back to the grindstone.
"When it did fire, everyone stopped, stood by it, and they were like, 'Yes!'" he says. "Then the energy level went, voom, right back up."
Each team member had a focus. Reckow was the designated fabricator, cutting metal and welding where it was needed, figuring out how incomplete body panels and trim pieces would fit, and supervising the overall project. Clouse homed in on getting the engine together and running, while Phillips spent a lot of his time on the doors and interior and Lirones got the brake system and lights working. But they all supported one another as the project moved along, so there was a lot of cross-pollination, so to speak.
As the four men worked—supported at intervals by other Hagerty employees, friends, and a fan or two—a group of onlookers clotted around the canopy to see how the project was progressing. A man in a Marine Corps hat who seemed to know a lot about the Model A stuck around nearly the entire time, offering bits of useful information and advice here and there. His wife, also a helpful type, even appeared with parts they couldn't find from time to time (albeit from Hagerty's own dense pile).
Hagerty's media staff maintained ceaseless vigilance over the company's social media and YouTube accounts, which were feeding live coverage of the build to the public. Occasionally, someone watching online would post a comment on how something fit or outlining a procedure, which the media team relayed to the mechanics.
The result, by Friday afternoon, was a running, driving, Beverly Hillbillies-style jalopy. All told, including a day of parts-scouting, the build took four days. On Saturday, the team hit the local highways, covering almost 300 miles in a couple of days.
Unfortunately, the Model A didn't make it all the way back to Michigan under its own motivation. An oil leak, a fried starter, and a few other mishaps delayed the trip too much, and the team had to get back home to their "real" jobs and families. So the car ended up on a trailer for the remaining 400 miles or so to Traverse City. A few miles before it arrived at Hagerty's headquarters building, the team unloaded the car from the trailer, push-started it, and drove it the rest of the way for a symbolic finish.
"I consider the Swap to Street build a total success, even though we did have to trailer it the rest of the way home," Reckow said. "We proved that it can be done, and hopefully we’ve inspired other people to try a project of their own."
